We had our heat worked on several weeks ago. One of the guys left an interesting tool one day. I immediately took it into my studio to see what it would do. (I did give it back the next day!) It was a crimper, used for making heating ducts a little smaller, so they fit together well. Erwin's crimper was a three blade version, with a very nice handle. He says they don't make them any more. Too Bad.
I did find an assortment of them on the internet, and ordered one made by
Malco. It has five blades, they do also make three bladed crimpers. It feels very solid and has a nice handle. Today I was waiting for the inspector to check off the work, so I played with some copper. I used 24 gauge annealed copper for most of the tests. For one test I used tooling copper, which is around 30 gauge, and very soft. I sanded the copper pieces with 400 grit wet or dry sandpaper first. Then they were dipped in liver of sulfur, polished with a very soft brass brush. I repeat this until I like the color. Then I crimped in different patterns.
I like the look better than the metal crimpers that look like pasta rollers. (I have no idea what they're called.) This irregular texture is more appealing to me. However, it's a fairly large scale texture and might not work for jewelry. The crimps are about 1-7/8 inches long and 1/8th of an inch deep. It isn't a sharp fold in the metal. Below are the results. If you want to see these enlarged, check out my flickr photo set,
Testing.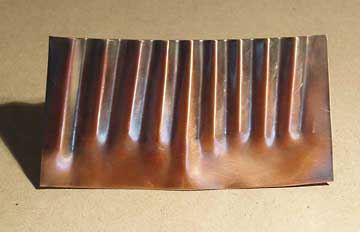
Sample one. This is the pattern I get crimping along one edge. This piece of copper is 24 gauge, about 4 inches wide.
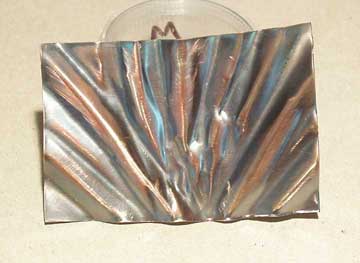
Sample two. I was trying for rays here. I think the three blade crimper would be better. This is 24 gauge copper, about 2.5 inches wide.
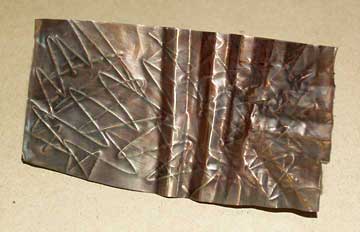
Sample three. This is a piece of tooling copper, about 30 gauge. I scribbled on the back with a ball point pen, then colored the metal with liver of sulfur, crimped from both sides, and colored the metal again. 4 inches wide.
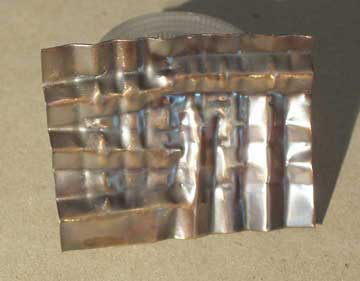
Sample four. I crimped from all angles, sometimes crimping over other crimps. 24 gauge copper, 2.5 inches wide.

This was sample four, hammered almost flat. This one starts to get interesting to me. A little more crimping and hammering might make it very nice.
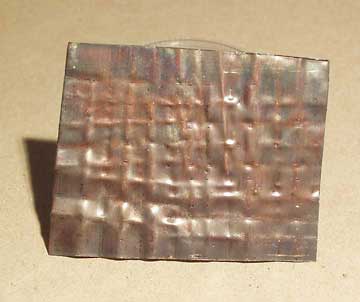
Here is the back of sample four, I think it could be interesting with a little more sanding and coloring.
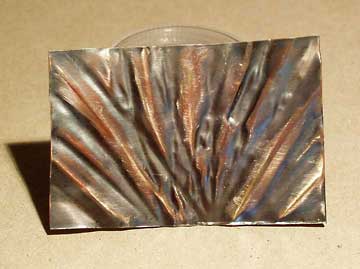
And this is sample two, hammered almost flat.
Labels: Experiments, Tools